Whenever glass has been altered or shaped by exposure to a torch flame, you can be sure that stresses have been introduced. We can reduce some of these stresses by hand annealing. Glass apparatus should never be put into laboratory service unless it has been properly annealed! We also believe no art glass with all the colors should ever be sold without proper annealing of the glass.You can not see glass stress with the naked eye, so glassblowers use a device called a polariscope to visualize the strains/stresses. With a polariscope, you can check out your seals before and after annealing. The more complicated the seal or weld, the more likely there will be stresses harmful to the final product and its users. Over time cracks can occur that seemed perfectly clean. If you don't have a polariscope.
Flame Annealing
You can use a soft, bushy cool flame to "brush" away the stress areas located in and around the area of your fire polish and other seals that you make. Think of your flame as an artists paint brush or sandpaper working on bondo if you have ever done car bodywork. The strain needs to blend into the surrounding glass smoothly, with no jagged edges. The process should take approximately two minutes for the simple and small glass pieces you are working with. The annealing flame will often leave a black sooty residue that is carbon buildup which can be wiped away with a soft cloth once the glass has cooled:
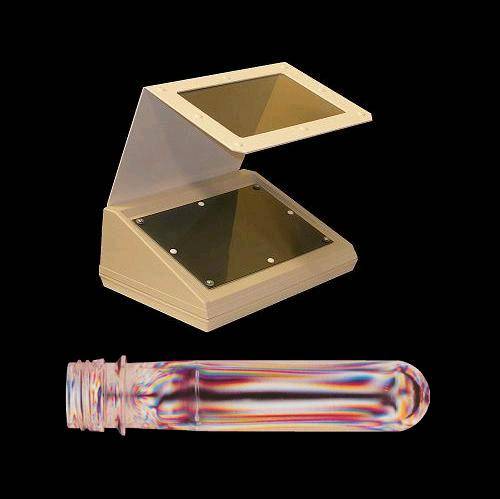
The Corning Museum of Glass has a web page with an excellent video that demonstrates stress in unannealed and properly annealed objects.